by Juliet Nanyonga & Simon Bosch
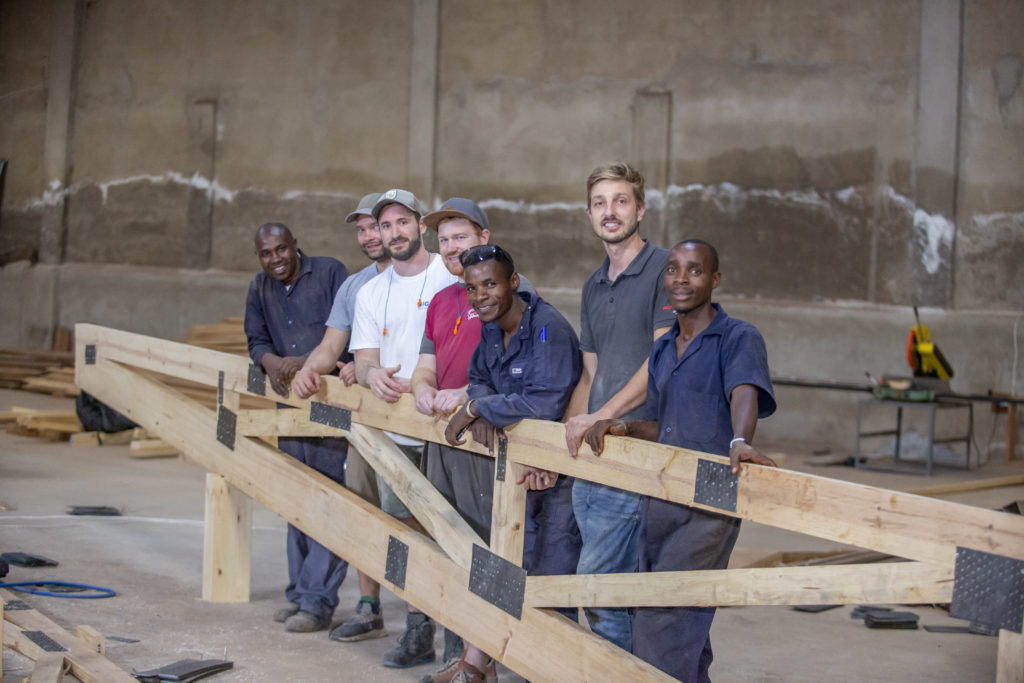
In 2018, the Mass Timber Construction Project (MTCEA) was launched with the goal of creating pathways for sustainable mass timber construction in East Africa. This project included research into the timber value chain in Uganda and the development and improvement of sustainable mass timber value chains in the region. As a result of the MTCEA, Fairventures Worldwide and its partners developed a production line of engineered wood products. In order to demonstrate the practical applications of these products, the Timber Innovation Centre (TIC) was established. The TIC has enabled a learning experience in terms of the workability of the products, potential gaps in the production line, and costs in comparison to other building materials. Furthermore, the TIC is an ideal observation point to assess the durability of the engineered wood products, maintenance costs, and other data that can inform future timber construction projects.
At the beginning of December 2022, the development permit for the TIC project was received, which marked the commencement of its activities. The initial step was demolishing existing concrete posts that were protruding from the columns, which were embedded beneath the concrete slab base of the roof terrace. Steel works for the primary structure, to connect the TIC to the existing building, were carried out within three weeks. Following this, the project proceeded with the use of wood.



Timber Sourcing
The pine timber that is available on the Ugandan market is not suitable for use in structural construction due to its inconsistency in quality and moisture content, which makes it unstable and unreliable. Therefore, for this project, all timber used was sourced from Busoga Forestry Company (BFC), a subsidiary of Green Resources located in Jinja. Following the sourcing, the Glue Laminated Timber (Glulam) was manufactured. The press used for this was mechanical and could only produce two beams per day, thus the whole process took two weeks. The beams and timber were transported to the Workshop for prefabrication.



Prefabrication in the Workshop
During this project, prefabrication, a building system in which significant sections or components are created off-site in a workshop or factory, was utilized, resulting in more than 60% of the work being done off-site. This was done with the intention of reducing costs and creating consistency through quality control. Furthermore, as the Timber Innovation Centre is an exhibition building, prefabrication would also allow for it to be moved to other locations for showcasing.
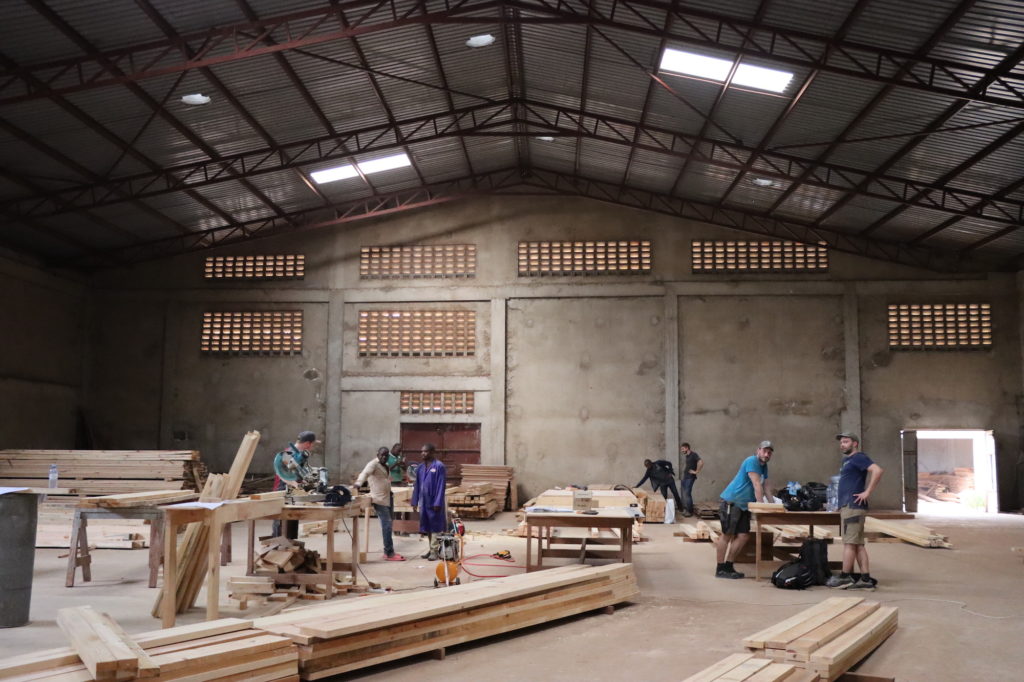
In the workshop, glulam beams, columns, and roof trusses were cut with precision in order to ensure a perfect fit during the final assembly. The walls were constructed of 18mm plywood held in timber frames of 50x100mm section. Gypsum boards of 9mm were then screwed onto the interior face for fire and water protection, as well as to create accent walls. The 50mm by 100mm timber connected to the steel foundation was treated with (Benzothiazol-2-ylthio)methyl thiocyanate (TCMTB) in an isolated section of the workshop. Three layers of TCMTB were brushed consecutively on the timber and allowed to dry for 8 hours. The remaining timber visible in the design was treated with linseed oil, including the beams, columns, and the tongue and groove for cladding. All elements, roof trusses and timber were then transported to the site for assembly.


Wall Cross Section & Floor Section
For roofing, 50x100mm wooden pieces are used for purlins to which 0.4mm thick iron sheets with polynum insulation are screwed. In the office section, a tongue and groove wooden ceiling below the trusses has been installed. At the multipurpose section, the roof trusses will be exposed to showcase the craftsmanship and the glulam beams.
Assembly on site


Testing solid pine, finger jointed timber, and Glue Laminated Timber
Samples of the manufactured beams and timber were taken to Makerere University’s School of Forestry in order to compile a materials test report. This report is to assess the physical and mechanical properties of solid, finger-jointed and glue laminated timber. The results of these tests are essential for engineers to understand the capabilities of the wood products in structural applications. This report has been compiled and is ready for stakeholder review and engagement.



Test samples at the Laboratory
Challenges in implementation
The wood construction project faced multiple challenges, from delayed building and development permits, to materials not being readily available on the market and difficulty in finding carpenters skilled in wood construction and onsite joinery. The team overcame these issues by looking for substitute materials, placing custom orders and training interested and practicing local carpenters to work with.
Furthermore, there was a lack of treatments that were environmentally friendly and offered long-term protection against weathering and biodegradation. The rains set in at the beginning of March when roofing was just being started which exposed the roof trusses and interior face of the wall elements. At this point in the assembly phase the primary floor was covered with a waterguard tarp and a moisture proof tarp was already stapled onto the walls.
Opportunities
By promoting timber in construction, numerous wood products can be used, thereby creating and increasing demand, ultimately resulting in the empowerment of the sector. Products such as flooring, ceiling, roofing, furniture and framing can uptake timber flooded on the local markets.
The Timber Innovation Centre has become a demonstration for the strength and dimensional capability of engineered wood products to professionals in the building space.
Conclusion
In order to realize sustainable and affordable housing constructed from wood in East Africa, it is necessary to focus on strengthening the timber value chain through improved infrastructure, education, research and development.
Education should range from skills and capacity building in onsite joinery, wood testing and grading to safety on construction sites and in using woodworking tools. This should extend to developing wood construction curriculums in tertiary institutions.
Research and development in wood treatment, product development, timber source tracing and forestry management practices should be done and documented to improve the sector. Research and establishment of standards from milling to site assembly is also required in order to improve its use in structure and design.
Infrastructure development and improvement is needed such as fully equipped wood testing facilities, kilns and engineered wood production lines.